Comprehensive Guide: What is Porosity in Welding and Exactly How to stop It
Comprehensive Guide: What is Porosity in Welding and Exactly How to stop It
Blog Article
The Science Behind Porosity: A Comprehensive Guide for Welders and Fabricators
Recognizing the detailed devices behind porosity in welding is important for welders and producers striving for impressive workmanship. As metalworkers delve into the midsts of this sensation, they reveal a world governed by numerous factors that affect the development of these small spaces within welds. From the make-up of the base products to the intricacies of the welding process itself, a multitude of variables conspire to either aggravate or ease the existence of porosity. In this extensive overview, we will certainly unwind the science behind porosity, exploring its effects on weld high quality and introduction progressed methods for its control. Join us on this journey through the microcosm of welding blemishes, where precision meets understanding in the pursuit of remarkable welds.
Recognizing Porosity in Welding
FIRST SENTENCE:
Exam of porosity in welding exposes crucial insights into the honesty and high quality of the weld joint. Porosity, identified by the presence of tooth cavities or voids within the weld steel, is an usual issue in welding procedures. These voids, otherwise effectively addressed, can jeopardize the architectural integrity and mechanical properties of the weld, causing possible failures in the completed item.
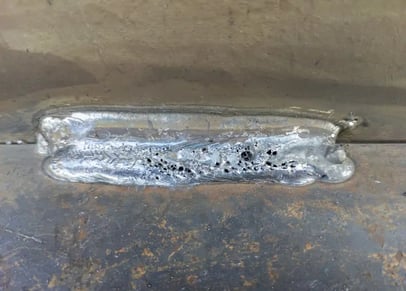
To spot and quantify porosity, non-destructive testing methods such as ultrasonic testing or X-ray inspection are usually used. These strategies permit for the identification of internal defects without endangering the honesty of the weld. By assessing the dimension, form, and circulation of porosity within a weld, welders can make educated decisions to improve their welding procedures and accomplish sounder weld joints.
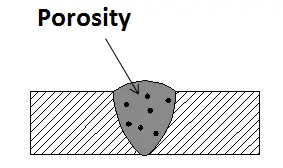
Elements Influencing Porosity Development
The occurrence of porosity in welding is affected by a myriad of elements, ranging from gas protecting performance to the details of welding parameter setups. Welding criteria, including voltage, current, travel rate, and electrode kind, additionally influence porosity development. The welding technique employed, such as gas steel arc welding (GMAW) or secured steel arc welding (SMAW), can affect porosity formation due to variants in warm distribution and gas coverage - What is Porosity.
Effects of Porosity on Weld Quality
The existence of porosity additionally compromises the weld's resistance to deterioration, as the trapped air or gases within the spaces can respond with the surrounding environment, leading to degradation over time. Furthermore, porosity can prevent the weld's capability to hold up against stress or influence, more jeopardizing the general quality and reliability of the welded structure. In important applications such as aerospace, auto, or architectural building and constructions, where security and sturdiness are critical, the harmful results of porosity on weld top quality can have serious effects, stressing the significance of reducing porosity with appropriate welding methods and procedures.
Techniques to Reduce Porosity
Furthermore, utilizing the suitable look at these guys welding specifications, such as the correct voltage, present, and travel speed, is crucial in avoiding porosity. Maintaining a regular arc size and angle during welding also assists minimize the possibility of porosity.

Making use of the appropriate welding technique, such as back-stepping or employing a weaving activity, can additionally aid distribute heat equally and reduce the opportunities of porosity development. By applying these strategies, welders can effectively reduce porosity and create premium welded joints.
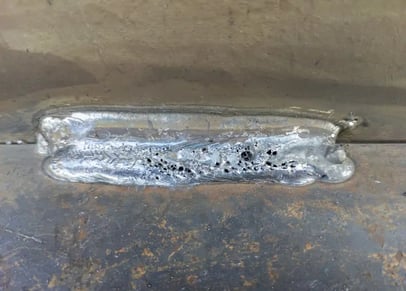
Advanced Solutions for Porosity Control
Applying innovative modern technologies and ingenious methods plays a pivotal duty in accomplishing superior control over porosity in welding processes. One sophisticated option is making use of advanced gas mixtures. Securing gases like More Bonuses helium or a mix of argon and hydrogen can help reduce porosity by supplying much better arc stability and boosted gas coverage. In addition, using sophisticated welding methods such as pulsed MIG welding or changed environment welding can likewise assist minimize porosity issues.
One more advanced service involves using innovative welding tools. For circumstances, utilizing tools with integrated features like waveform control and innovative power sources can boost weld high quality and minimize porosity risks. The application of automated welding systems with specific control over specifications can dramatically reduce porosity flaws.
Furthermore, integrating innovative surveillance and evaluation modern technologies such as real-time X-ray imaging or automated ultrasonic screening can help in identifying porosity early in the welding procedure, enabling prompt restorative actions. In general, integrating these sophisticated remedies can substantially boost porosity control and improve the general quality of bonded elements.
Final Thought
Finally, understanding the scientific research behind porosity in welding is go to this website essential for welders and makers to create premium welds. By recognizing the variables influencing porosity formation and applying methods to minimize it, welders can enhance the total weld high quality. Advanced services for porosity control can additionally improve the welding procedure and make sure a strong and trusted weld. It is crucial for welders to continuously enlighten themselves on porosity and execute finest methods to achieve optimum results.
Report this page